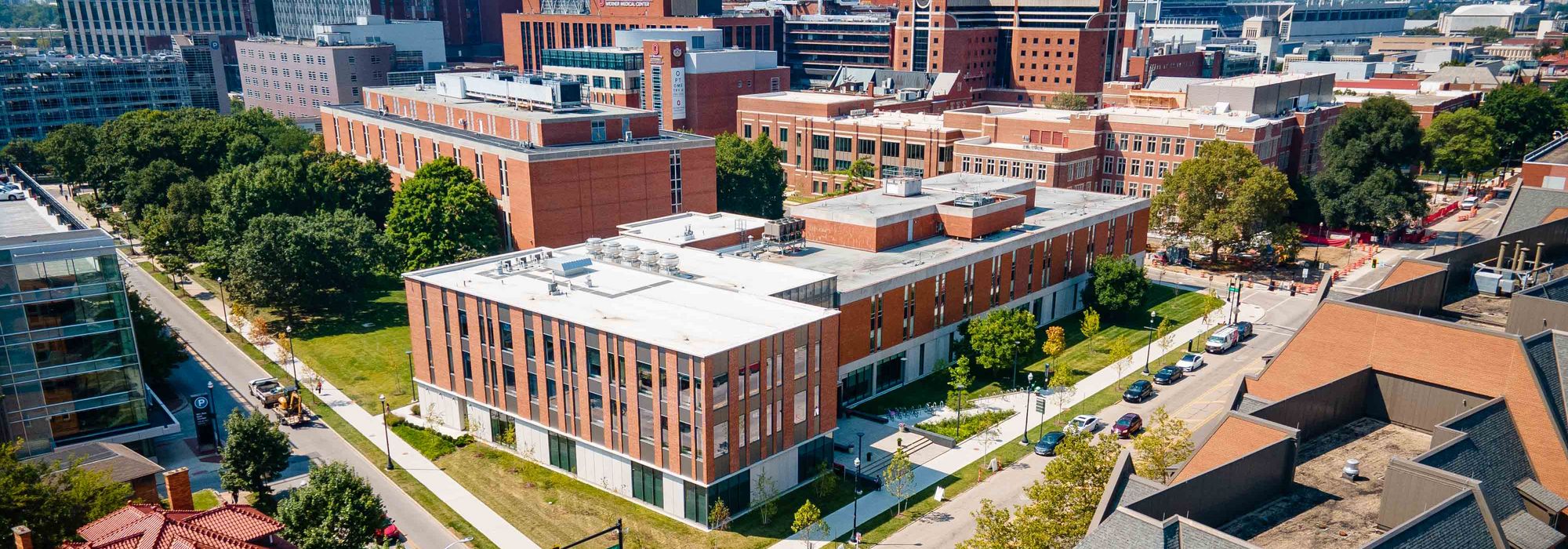
About Jane E. Heminger Hall
Jane E. Heminger Hall supports The Ohio State University College of Nursing’s vision to be the world’s leader in thinking and achieving the impossible in order to transform health and improve lives.
The new, 40,161 gross square foot structure, which is located on the south side of Newton Hall, serves as a gateway to the university’s health science campus. It further positions us as healthcare leaders by supporting critical pillars of our college: academics, research, innovation and evidence-based practice (EBP).
Inside the new entrance on Neil Avenue, a three-story glass atrium links our new building to Newton Hall and creates an open and inviting space to promote collaboration and transdisciplinary learning. The new structure adds spacious classrooms and learning environments, faculty offices and research and EBP centers. There are new program spaces, which include a multi-purpose dividable classroom and events center, flat flexible classrooms, group study rooms, a makerspace and a demonstration kitchen. The outside features bicycle parking and a beautifully landscaped outdoor patio and garden.
The new building will also become the first LEED and WELL-certified building on Ohio State’s campus. The WELL v2 Building Standard, created and administered by the International WELL Building Institute, is a performance-based system for measuring, certifying and monitoring features of a building’s environment that impact human health through air, water, nourishment, light, movement, sound, materials, mental health, thermal comfort, community and innovation. Learn about the WELL features employed in the project here.
Jane E. Heminger Hall was designed by signature design firm ikon.5 architects, ranked as the sixth-best design firm in the United States and winner of more than 75 national and international awards, in partnership with Architect of Record M+A Architects, known for their knowledge of and expertise in projects for The Ohio State University.
Will you join us as we build dreams, discover solutions and deliver impact? Your commitment will be reflected in the next generation of inspired healthcare leaders. We look forward to your support as we transform the future of health.
LEED Certification
Learn more about the requirements and our strategies to achieve LEED certification.
- Location and Transportation
-
Access to quality transit
Requirement: Locate any functional entry of the project within a quarter-mile walking distance of an existing or planned bus stop, or within a half-mile walking distance of existing or planned bus rapid transit stops, light or heavy rail stations or commuter rail stations.
- The bus services meet the minimums listed below:
- 144 weekday trips and 108 weekend trips.
- Qualifying transit routes must have paired route service (service in opposite directions).
Our strategy: There are three bus lines and shuttle services within a quarter mile, for approximately 142 weekday trips and 126 weekend trips:
- COTA buses (Central Ohio Transit Authority)
- Wexner Med Center Shuttles have stops within a quarter of a mile (48 and 26 weekday trips, respectively). Overnight & Weekend Shuttle has two stops within a quarter of a mile (7 weekday trips and 54 weekend trips).
- CABS (Campus Area Bus Service) are available within a quarter of a mile. Since the project is served by more than two transit routes, and no one route provides more than 60% of the documented requirements, the project earned some extra points.
- Sustainable Sites
-
Open space
Requirement: Provide outdoor space greater than or equal to 30% of the total site area (including building footprint). A minimum of 25% of that outdoor space must be vegetated (turf grass does not count as vegetation) or have overhead vegetated canopy.
Our strategy: Based on a total site area of 52,000 square feet, outdoor space is greater than 15,600 square feet and 3,900 square feet must be vegetated (not turf grass) or have tree canopy. Outdoor space is physically accessible and fulfills the following: pedestrian-oriented paving or turf area with physical site elements that accommodate outdoor social activities, garden space with a diversity of vegetation types and species that provide opportunities for year-round visual interest, and preserved or created habitat that meets the criteria of this credit and includes elements of human interaction. Based on LEED/WELL project boundary:
- total site area of +/-52,000 square feet
- total building +/-12,870 square feet
- total hardscape +/-12,180 square feet
- total greenspace of +/-26,950 square feet
- equals +/-52% pervious, 48% impervious
The site design accommodates the College of Nursing’s vision with a variety of exterior spaces that encourage interaction with the environment, social interaction, passive recreation and physical activities. The building fronts Neil Avenue, a major campus street with a host of campus activities and multi-modal transportation access. A main entrance plaza features hardscape and landscape areas to accommodate circulation, seating, viewing and bike parking with access to the Neil Avenue streetscape and wide pedestrian sidewalk. The plaza serves as a main entrance and foreground to the interior “winter garden” (the Atrium), which serves as the major defining interior orientation, special event and circulation space of the building and college. Landscape plantings provide seasonal visual interest and shade, with accent lights highlighting the entry. To the west of the Atrium, an exterior terrace accommodates informal gatherings as well as more structured outdoor education and special events. An open lawn area accessed from the terrace provides a view of the natural campus landscape, while accommodating special events areas for tents and other overflow uses. The south side of the building features a tree grove and sloped lawn which buffers the W. 9th Street activities, provides a natural foreground to the auditorium and visual access to nature from within the building.
- Water Efficiency
-
Outdoor water use reduction
Requirement: Reduce outdoor water use through one of the following options: Option 1. No irrigation required - Show that the landscape does not require a permanent irrigation system beyond a maximum 2-year establishment period.
Our strategy: The plants that comprise the design were selected from a list of Ohio native and adapted plant species known for drought tolerance and durability within the climate zone of the project. Natural precipitation supplemented by manual irrigation will be used for the initial establishment period of the plant material. When natural precipitation does not provide the estimated average requirement of one inch of precipitation per week, manual irrigation will be used to establish the plant material. Permanent irrigation is not included as part of the project.
Indoor water use reduction
Requirement: For the commercial fixtures, fittings and appliances, as applicable to the project scope, reduce aggregate water consumption by 20% from the baseline. All newly installed toilets, urinals, private lavatory faucets and showerheads that are eligible for labeling must be WaterSense labeled. Install appliances, equipment and processes within the project scope that meet the requirements listed in the tables below:
- Baseline water consumption of fixtures and fittings (*WaterSense label available)
- Water closets (toilets)* = 1.6 gallons per flush (gpf)
- Urinal* = 1.0 gpf
- Public lavatory (restroom) faucet = 0.5 gallons per minute (gpm) at 60 pounds per square inch (psi)
- Private lavatory faucet* = 2.2 gpm at 60 psi
- Kitchen faucet (excluding faucets used exclusively for filling operations) = 2.2 gpm at 60 psi
- Showerhead* = 2.5 gpm at 80 psi per shower stall
- Standards for appliances:
- Residential dishwashers (standard and compact) = ENERGY STAR or performance equivalent
- Prerinse spray valve ≤ 1.3 gpm
Our strategy: The project has achieved a percent water use reduction of 32.66% from the baseline. All newly installed toilets, urinals and private lavatory faucets that are eligible for labeling are WaterSense labeled. Appliances are ENERGY STAR or equivalent where required.
- Baseline water consumption of fixtures and fittings (*WaterSense label available)
- Energy and Atmosphere
-
Fundamental commissioning
Requirement: The Commissioning Agent must have documented commissioning process experience on at least two building projects with a similar scope of work. The experience must extend from early design phase through at least 10 months of occupancy. Complete the following commissioning process activities for mechanical, electrical, plumbing and renewable energy systems and assemblies in accordance with ASHRAE Guideline 0–2005 and ASHRAE Guideline 1.1–2007 for HVAC&R (Heating, Ventilation, Air Conditioning and Refrigeration) systems, as they relate to energy, water, indoor environmental quality and durability:
- Review contractor submittals.
- Verify inclusion of systems manual requirements in construction documents.
- Verify inclusion of operator and occupant training requirements in construction documents.
- Verify systems manual updates and delivery.
- Verify operator and occupant training delivery and effectiveness.
- Verify seasonal testing.
- Review building operations 10 months after substantial completion.
- Develop an ongoing commissioning plan.
Enhanced commissioning
Requirement: Fulfill the requirements in Fundamental Commissioning and Verification as they apply to the building’s thermal envelope in addition to mechanical and electrical systems and assemblies. Complete the following commissioning process activities for the building’s thermal envelope in accordance with ASHRAE Guideline 0–2005 and the National Institute of Building Sciences (NIBS) Guideline 3–2012, Exterior Enclosure Technical Requirements for the Commissioning Process, as they relate to energy, water, indoor environmental quality and durability.
Our strategy: Commissioning authority has documented commissioning process experience on multiple building projects with similar scope of work. All downstream equipment is included in the scope of this credit (e.g., heat exchangers, steam pressure reduction stations, pumps, valves, pipes, building electrical services and controls.) All upstream equipment associated with serving the building is included in the scope.
Envelope commissioning
Additionally, envelope commissioning has been performed for the building’s thermal envelope in accordance with ASHRAE Guideline 0–2005 and the National Institute of Building Sciences (NIBS) Guideline 3–2012, Exterior Enclosure Technical Requirements for the Commissioning Process, as they relate to energy, water, indoor environmental quality and durability.
Optimize energy performance
Requirement: Establish an energy performance target no later than the schematic design phase. The target must be established as kBtu per square foot-year of source energy use. Option 1. Whole-building energy simulation – Analyze efficiency measures during the design process and account for the results in design decision making. Use energy simulation of efficiency opportunities, past energy simulation analyses for similar buildings, or published data (e.g., Advanced Energy Design Guides) from analyses for similar buildings. Analyze efficiency measures, focusing on load reduction and HVAC-related strategies (passive measures are acceptable) appropriate for the facility. Project potential energy savings and holistic project cost implications related to all affected systems. Project teams pursuing the Integrative Process credit must complete the basic energy analysis for that credit before conducting the energy simulation.
Our strategy: Energy simulation performed during design resulted in a total energy cost savings (excluding site-generated renewable energy) of 28.4%.
- Materials and Resources
-
Building product disclosure and optimization – sourcing of raw materials
Requirement: Use products sourced from at least three different manufacturers that meet at least one of the responsible extraction criteria below for at least 20%, by cost, of the total value of permanently installed building products in the project.
Our strategy: The design team intentionally selected products and materials that have recycled content, have take-back programs and are locally sourced. During construction, the contractors verified and selected materials that fulfilled both the design intent and this criterion. For instance, the coarse and fine aggregate for the concrete came from within 100 miles of the project site.
- Indoor Environmental Quality
-
Low-emitting materials
Requirement: Product manufacturing and project teams consider levels of volatile organic compound (VOC) emissions into indoor air and the VOC content of materials, as well as the testing methods by which indoor VOC emissions are determined. Different materials meet their respective requirements to be considered compliant. The building interior is organized into categories, each with different thresholds of compliance. The building interior is defined as everything within the waterproofing membrane.
Our strategy: The design team intentionally selected products and materials that had no or low VOC content and were healthy for occupants. During construction, the contractors verified and selected materials that met the design intent. Many products used by the project have third-party certifications that verify they meet air quality standards for this project.
Indoor air quality assessment
Requirement: Conduct a “flush out,” whereby all interior finishes, such as millwork, doors, paint, carpet, acoustic tiles and movable furnishings (e.g., workstations, partitions), must be installed and major VOC punch list items must be finished.
Our strategy: This project used the flush out option, before occupancy, such that all filters were replaced and a flush out was performed. The flush out occurred by supplying a total air volume of 14,000 cubic feet of outdoor air per square foot of gross floor area while maintaining an internal temperature of at least 60oF and no higher than 80oF and relative humidity no higher than 60%.
- Innovation
-
Our Strategy: The College of Nursing held open houses and tours of Jane E. Heminger Hall when the building opened in fall 2022 for donors, alumni and employees. These featured main design elements of Jane E. Heminger Hall. In addition, the college created, in consultation with our architects, a quarter-mile Wellness Walk that winds through all three floors and the length of the two adjacent College of Nursing buildings: Newton Hall and Jane E. Heminger Hall, utilizing the grand stairs of Jane E. Heminger Hall. The walk is punctuated with wellness nodes that feature:
- a QR code to connect walkers to our LEED and WELL educational information online and the number of steps (in either direction) to the next Wellness node, and
- quotes to inspire not only our students, faculty and staff, but also our alumni and visitors.
Prominent signage explaining LEED and WELL is located in the Atrium of Jane E. Heminger Hall, and features the QR code to connect readers to our LEED and WELL educational information on the website for Jane E. Heminger Hall and a map of the Wellness Walk. The QR code is available in other locations as needed.
- Regional Priority
-
Surrounding density
Requirement: Locate on a site whose surrounding existing density within a quarter-mile radius of the project boundary meets the values the following: Residential density (DU/acre) = 12 and non-residential density (FAR) = 0.8.
Our strategy: located as noted above.
Diverse uses
Requirement: Construct or renovate a building or a space within a building such that the building’s main entrance is within a half-mile walking distance of the main entrance of many existing and publicly available diverse use buildings.
Our strategy: The project is located in an urban campus area, where there are both a high density of buildings and a wide array of building types within walking distance. The latter include banks, convenience stores, pharmacies, entertainment centers, hair care places, hospitals and medical offices/clinics, libraries and parks.
Heat island reduction
Requirement: Area of nonroof measures/0.5 + area of high-reflectance roof/0.75 + area of vegetated roof/0.75 ≥ total site paving area + total roof area
Our strategy: A combination of high-reflectance roofing and high albedo paving (concrete) help to reflect the sun’s heat back up into the atmosphere instead of being absorbed in dark/low albedo paving (asphalt).